Paper Machine Equipment
JMC Papertech is promoted by group of experienced
industrialist and Technocrats with successful track record and reputation. Initially
company was involved in heavy fabrication and vessels and later on switched
over to machineries for cement industries. Later on company started
manufacturing spherical rotary Digester, fabricated drying cylinders and
M.S. Yankee Cylinders on demand of paper industries. On the constant demand
of these Cylinder, Paper industry encouraged company to start fabrication of
other machine pats and with their support and technical know- how from paper
mill designers, company successfully started manufacturing complete Plant
for making all Type of paper up to capacity of 10 -200 TPD
Baskets
Perforated or Slotted Step Rotor
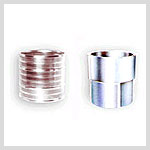
Ask for Price
Salient
Features
- Suitable for operation with large flat shaped contaminants.
- Special design features avoid string formation.
- Rotor edges hard faced.
- Hole or slot screen basket.
- Dynamically balanced rotor.
JMC Low (LC)
Consistency Screen
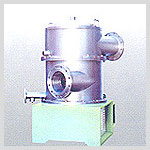
Ask for Price
Salient
Features
- Vertical screen designed for fine screening of all kind of stock
suspensions at low consistency range of 0.4 -1.1 %.
- The screens are suitable for stock preparation system and also for
approach flow system ahead of paper machine.
- The Multivane Aerofoil Rotor design ensures the screen to operate
free from pulsation.
- Low power consumption.
- Exceptional improvement in screening efficiency.
- Improve quality of paper.
- Dependable paper machine operation.
- Basket-hole or slott type
- Excellent manufacturing fitness.
Model No. |
Hydraulic LPM |
Capacity* TPD |
Motor Rating: KW |
JSVL 04 |
2500 |
40 |
15 |
JSVL 05 |
7000 |
110 |
30 |
JSVL 08 |
12000 |
160 |
37 |
JSVLW 04 |
2000 |
|
|
* Depending on stock, grade, consistency and screen perforation / screen
slot application
- J-JMC
- S-Screen
- V-Vertical
- M- Medium Consistency
- W- Washing Cycle
- Present manufacturing range other models are under development.
Baskets
Perforated or Slotted Foil Rotor
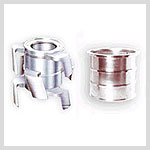
Ask for Price
Salient
Features
- Multi vane aerofoil rotor.
- Pulsation frees rotor design.
- Special rotor design avoids string formation.
- Gentle screening.
- For low consistency hole or slot basket
- Dynamically balanced rotor.
Centricleaners
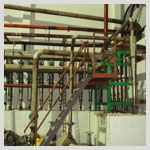
Ask for Price
Salient
Features
- Effective removal of Sand, unbeaten paper chips hard Cooked fibers
and other no fibrous heavy materials
- Low fiber rejection
- Low Pressure drop
- Fabricated from SS 304 and 316 Material
- Intel Tapered Headers with pulp valve in SS construction
- Available in 500 and 1000 LPM throughput
- Fibber recovery arrangement in Last Stage
Stock Chest
Agitators (AG)
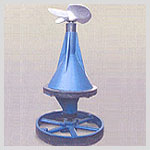
Ask for Price
Energy
efficient agitators find application in all type of Pulp storage chests,
including Hight Density Towers, Mixing Chest & Machine Chest.
The sturdy design incorporate Bearings & Glands. Located outside,
optimally designed adjustable propeller blades. All parts coming in contact
with stock made of stainless Steel, the agitators are highly energy
efficient and have the provision for adjusting the vane angle to suit
specific process requirement of gentle or strong agitation.
Salient Features
Agitator Size |
Horizontal Chest |
Vertical Chest |
|
Volume (M3) |
Motor Rating (kW) |
Volume (M3) |
Motor Rating (kW) |
Vane Dia (mm) |
AG 50/60 |
25-100 |
11-15 |
7-15 |
5.5-7.5 |
500/600 |
AG 75/85 |
100-275 |
15-22 |
20-40 |
11-15 |
750/850 |
AG 100/115 |
275-500 |
30-37 |
45-80 |
18.5-22 |
1000/1150 |
AG 135/155 |
500-700 |
55 |
85-155 |
30-37 |
1350/1550 |
AG 170 |
700-850 |
75 |
155-200 |
45 |
1700 |
Stock Thickener
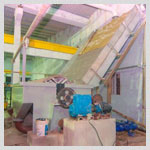
Ask for Price
Salient Features
- Decker Thickener compressing of CI/SS Moulds and MS/ SS Vat, are best
suited for removal of excess water from stock
- Sizes vary from 2.00 mtrs to 3.00 mtrs depending upon the process
capacity
- Input Consistency 1% out put consistency of 4%
- Minimum fiber loss due to modified cum washing purpose
- Constructed in SS 304 and SS 316 Material
- Driven with Variable Speed drive for setting the drainage of
different of stock
De-Inking Cell
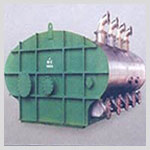
Ask for Price
The
purpose of de- inking is to remove the printing inks, stickies that might
effect the paper making process. In a de-inking process ink is detached from
fiber. Flotation technology provides high yield of fibers and simple
handling with maximum operating reliability.
Principle of Operation
The JMC De- inking cell consists of number of cells in series with
elliptical cross section with a baffle extending over the entire length to
separate suspension chamber from the foam collecting chamber. Air (at the
atmospheric pressure) and pulp stock is introduced into the cell through
injectors. Flow through nozzles generates vacuum which generators micro
turbulence resulting in widely ranging bubble sizes enabling efficient
removal of ink of particles. The enhances brightness to a high degree and
reduces dirt specks and stickies. The injectors optimize the quantity of the
air injected and the size of the bubbles generated.
The pulp stock freed ink is pumped from the bottom of one cell to the next
cell. The ink laden foam overflows to the foam chamber with the help of
motorized paddle. Flotation process is operated in a continuous mode and
helps to remove ink particles efficiency. Since the cells are interconnected
level is controlled through level transmitter on entire flotation machine.
The primary floatation stage ensures highest possible stock purity and the
secondary stage optimize yield. A Dearator cyclone removes air from the
stock and usable fibers are recovered from the foam.
Salient Features
- No sizing restrictions
- Single level control loop operation
- Optimized flotation yield at secondary stage without loss of
brightness and cleanliness.
- Very low fiber loss in the de-inking process as the foam is treated
in a cascade process.
- Optimize floatation yield at secondary stage without loss of
birghtness and cleanliness.
- Exceptional improvement in screening efficiency.
- Improve quality of paper
- Dependable paper machine operation
- Basket - hole or slott type
- Excellent manufacturing fitness